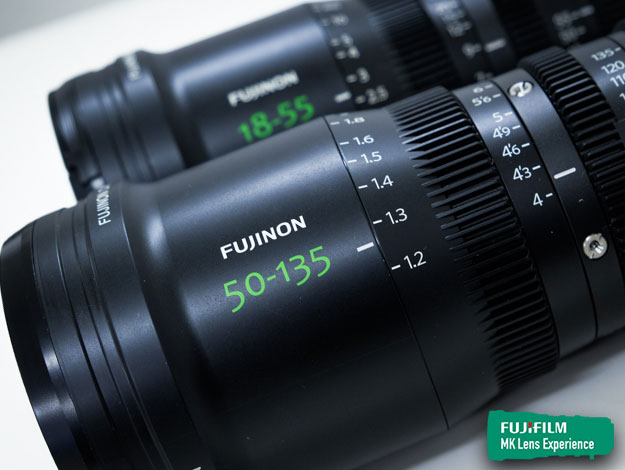
富士フイルムシネマレンズの光学性能、圧倒的な軽さ、思うがままの操作性、すべてを手にしたFUJINON MKシリーズ
富士フイルムのFUJINONレンズといえば世界のTV放送業界を技術で支えているトップブランドとして有名だが、シネマ業界でもFUJINONシネレンズというブランドで数々の驚くような製品開発を実現している。
2009年、世界初の4K映画用ズームレンズを発売。
2013年、シネレンズにドライブユニットを搭載可能にしてテレビの制作現場でも利用できるという常識を覆したZKシリーズを発売。
そして2017年、低予算だが映像品質には妥協しないという映像制作者をターゲットとしたFUJINON MKシリーズ(以下:MKレンズ)を発売。従来のコンパクトで軽量と言われているFUJINONシネレンズでさえも重量は2kg台だが、光学性能はそのままで1kg以下という新製品の実現は簡単なことではなかったはずだ。
FUJINON MKシリーズのMK18-55mmとMK50-135mmの開発背景についてお伺いした。
小型・軽量、そしてクリエイターが所有しやすい価格帯への挑戦
――MKレンズの開発目標と、それを伝えられた光学設計やメカ設計の方の率直な感想を教えてください。
野口氏(商品企画担当):MKレンズは、まず我々企画部門の方で主な仕様を決めて開発がスタートしました。主な仕様は、スーパー35mm/APS-Cセンサー専用設計で1kgを下回る小型・軽量化を実現すること。小型化という点では、レンズ前枠径は85mm、フィルター径は82mm、さらに0.8Mギアピッチの搭載を設計側に要求しました。
フィルター径を82mmと決めた理由は、大手量販店で購入できるものを使いたいという方が多かったためです。95mm径になると専門ショップに行かないと購入できません。そこで、池袋や新宿の大手量販店で購入できるフィルター径の最大のサイズである82mm径としました。
米澤氏(光学設計担当):企画部門から、性能はもちろん従来のFUJINONシネレンズのまま小型で1kgを切る重量、しかも操作感も維持と、光学設計に要求がありました。初めて聞いたときは非常に高いハードルだと思いました。従来のラインナップの中でも小型・軽量なXKレンズでさえも2.4kgです(ドライブユニット除く)そのような状況の中、レンズ単体で1kgを切るという企画ですので、実現は困難だと思いました。
川村氏(メカ設計担当):設計段階で目標部品としては1kgを切るようにというところからスタートしていますが、初めにメカ部品と光学部品それぞれの重さの目標値を割り付けて設計を進めていきました。実際に設計を初めてみると光学設計の制約からメカ部分で目標の重量を切るのは困難でしたが、メカ部品の比率を増やして光学部品の比率を下げてもらうなど、いろいろ検討をすることで最終的にはトータルで1kgを切った980gまで持ち込むことができました。
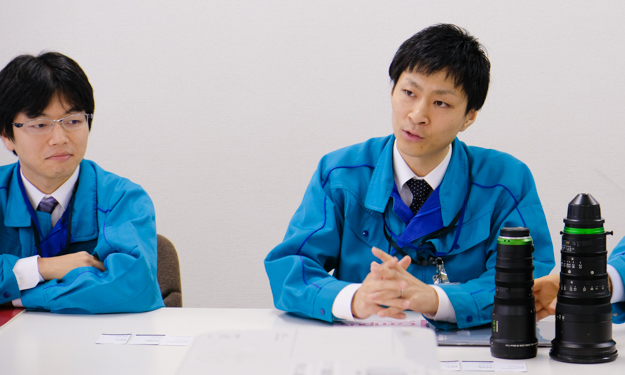
左から光学設計担当の田中氏と米澤氏
――2kg台のZKシリーズやXKシリーズからどのようにして小型化や1kg以下の軽量化を実現し、またどのような点に苦労したのかを教えてください。
米澤氏:前玉レンズの径は元々90mmぐらいありまして、それを60mm以下にしなければフィルター径は2本のレンズで共通化できませんでした。まずそれを目指して設計をしました。以前、スーパーハイビジョン用の8Kレンズを設計したことがあり、その際も前玉の径を小さくしならなければならないという課題がありました。そのときのズーム構成を応用することで、今回もレンズの径を小さくすることができました。
また、EDガラス(特殊光学ガラス)を数多く使用したことで色収差を抑制するとともに、小型・軽量化を実現しました。EDガラスはMK50-135mmで4枚、MK18-55mmで8枚使っています。小型化をしていくとどうしても一つひとつのレンズから発生する収差が大きくなってしまいがちです。収差を極力1枚1枚のレンズで抑えるためにEDレンズを数多く使用してこのサイズで性能を実現しました。
川村氏(メカ設計担当):メカ設計側としては、小型化でレンズが小さくなればなるだけレンズ鏡胴も小さくなり、フォーカス機構やズーム機構、絞り機構も合わせて小さくなるため、限られたスペースの中でいろんな調整機構をどうやって入れていくのかが難しいところになってきます。そのバランスをとるのが設計で困難な点でした。
また、今回のMKレンズは1kgを切る商品の実現と限られた部品費の兼ね合いで外装部品とレンズ保持部品の一部には樹脂を採用しました。しかし、最終的な商品は「樹脂製であることがわからなかった」と言われることがあるほどアルミに迫る外装の質感を実現できたと思います。この外装の質感の実現でもいろいろと苦労がありました。塗料との相性を工夫したり、樹脂の中にガラス繊維など入れて強度を向上させています。ガラス繊維は長さによってざらつき感が変化しますが、思考錯誤をして多くの候補の中から選定をして完成品の実現に至りました。
遠山氏(光学設計担当):樹脂を使うことによって光学設計側でも大変な苦労がありました。樹脂を使えば軽量化は実現できますが、どうしても温度に対する耐性が弱くなってしまいます。しかし、レンズ鏡胴が樹脂であっても今までのFUJINONシネレンズと同じ性能を出すのは必須課題でした。
この課題に対しては、設計段階からレンズ形状や硝材をどう組み合わせれば温度によるピントの変化を制御できるか解析を行いながらレンズ設計を追い込み、アルミ外装の従来機種と遜色のない品質を実現しています。
野口氏:メーカーとしては温度環境の変化に対してシビアに気を遣っています。例えば、MKレンズは温度の変化があったとしてもピントのズレによる性能低下は殆どありません。業務用の機材として過酷な環境で使用されることも想定して設計をしています。
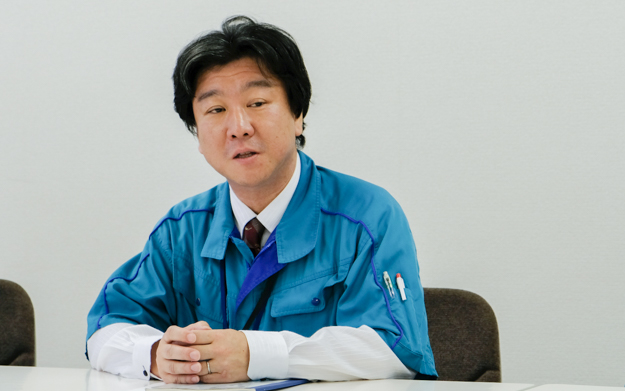
メカ設計担当の川村氏
――MKレンズの外装・質感を実現するうえでどのようなところに苦労しましたか?また、デザインのポイントなどを教えてください
酒井氏(デザイン担当):従来のHKレンズやZKレンズは、FUJINONシネレンズのフラグシップらしく鏡胴部はアルミ削り出し加工で「硬質な金属の無垢感」を訴求していました。黒く見えている部分が黒アルマイトという表面が硬い処理でして、緑に見えている部分もグリーンのアルマイトをあしらっています。
MKレンズは、FUJINONシネレンズの中でもエントリーシリーズであり、また軽量化の目的で樹脂を使っていますが、FUJINONシネレンズと統一したデザインを実現しました。従来のFUJINONシネレンズで定着してきた黒アルマイトの漆黒度やグリーンのアルマイトの見え方をMKレンズでも実現しています。特に困難だったのはアルミのアルマイトという処理の見え方を、MKレンズでは樹脂外装に塗装することで再現したところです。色味の漆黒度と黒アルマイト独特の光の回り方、ハイライトの回り方を塗料でどこまで表現できるか?特にグリーンアルマイトに顕著なのですけれど、このハイライトの回り方が、難しいところで調色を何度もトライしました。
このレンズは、レンタルではなく買い取りのお客様も増えると考えました。そこで自分で買ってたまに手に持って眺めて所有する喜びを楽しめるところも、アルミに迫る質感を実現することによって感じていただけるように意識しました。
![]()
上位機種と統一したデザインで、グリーンリングや黒のアルマイトを塗装で実現
操作性の面では、MKレンズはワンマンオペレーションでもお使いになられることを前提に、レンズは小さいけれども目盛りや数字はできるだけ大きくして、ワンマンオペレーションの操作時に表記が読み取りやすくなるように意識しました。
![]()
リングギアの数値は読み取りやすいように大きめに表記されている

左からデザイン担当の酒井氏と光学技術担当の柿沼氏
――MKレンズはこの価格帯で上位モデルと遜色のない品質が評価されていますが、品質を安定させるためにモノづくりの工程で何か新しい取り組みなどをしたことはありますか?
柿沼氏(光学技術担当):MKレンズでは調整工程のところで、手間をかけずに性能を満たせる仕組みを取り入れました。従来のFUJINONシネレンズは、解像性能を出すために長年腕を磨いた職人さんが時間をかけて組み立てを行い、難しい性能調整を実施していました。それをMKレンズから画期的な調整機構を導入し、事前に性能の自動判別ができるようになり性能出しのための調整作業が非常に短時間でできるようになりました。
MKレンズの生産工程では、光学設計ですとか、メカ設計、それから生産現場の人間も巻き込んで、いろいろアイデアを出して、新規調整機構及び新規設備の導入にチャレンジしました。
佐々木氏(光学技術担当):富士フイルムのシネレンズは、部品一点一点の精度はミクロンオーダーで作っています。特に4Kなどの高解像度になってくると、そこに最終的に求められる精度というのは非常に高くて、かつレンズ1本で構成する部品はレンズだけでも20枚以上にもなっています。まずは一個一個正確に作るというのはもちろんですが、最終的にそれが1本に組み合わさったときのバランスをいかにとっていくかというところは、ある意味1本1本オーダーメイド的に合わせ込んでいました。これが従来のシネレンズの組み立て工程です。
今回のMKレンズは基本的に従来のシネレンズから性能を一切妥協していませんが、従来のオーダーメイド的な作り方をどのように早く正確に作るかというところを改善しています。ここの部分の作り方は残念ながら詳しくご説明はできませんが、製造の初期段階の時点で「最終的にこういうレンズ性能になる」と予測できる仕組みを導入し、短時間で高品質のものを実現できるようになっています。
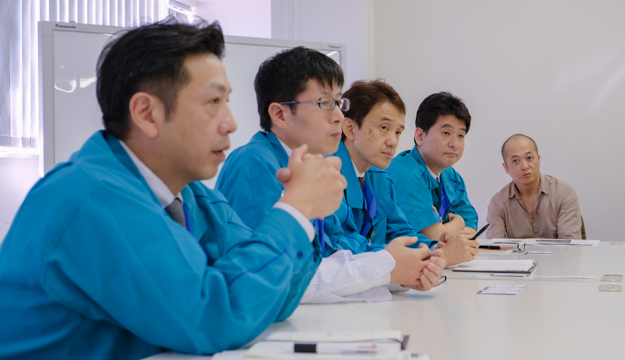
左から商品化担当の大野木氏、メカ設計担当の武田氏、光学設計担当の遠山氏、光学技術担当の佐々木氏、デザイン担当の酒井氏
スチル専用レンズと動画専用レンズは異なるもの
――低予算やワンマンオペレーションの映像制作の現場では、スチルレンズで動画の撮影が行われているのが一般的です。しかし、スチルレンズで動画撮影を行う場合、多くの制約が存在します。まず、スチル用のズームレンズは、ズームで像の大きさを変えると結像位置も変化してしまいます。MKレンズはこのズーム時の焦点移動をどのように抑制されていますか?
米澤氏:まず、スチルレンズでなぜ焦点移動が起こるのかというと、一般的なスチルレンズは、ズーム群とフォーカス群を同じ群で兼用することでレンズの小型化を図っているためです。そのためズーム時にフォーカス群が動いてしまい、焦点移動が起きます。一方シネレンズは、ズーム時の焦点移動を抑制するために、ズーム群とフォーカス群を分ける方式を採用しています。そのため、筐体が少し大きくなってしまいますが、ズーム時にフォーカス群の位置は変化しません。このようなレンズ構成によってズーム時の焦点移動を抑制しています。
MKレンズのレンズ構成は上位機種のZKシリーズやXKシリーズと同じ構成で、レンズの形や大きさ、位置が違うぐらいです。ズーム群の前側に、ズーム時に動かないフォーカス群があり、ズーム群、絞りがあって、絞りの後ろの群も動かない構成になっています。ズーム時の焦点移動は、この構成を採用することによって抑制しています。
――スチルレンズで動画撮影を行う場合はフォーカス調整するたびに画角変動(ブリージング)や光軸ずれも問題となります。MKレンズではブリージングや光軸ずれをどのように抑制していますか?
米澤氏:ブリージングも先ほどのズーム構成にまつわる話です。一般的なスチルレンズはフォーカスとズームを兼ねています。そのため、フォーカスを変えたときにどうしてもズームが変化してしまい、画角が変わってしまう構造になっています。MKレンズの場合はズームとフォーカスを独立して制御できます。それによりフォーカスを変えてもズーム群が動かないため、画角変動を抑制できます。
柿沼氏:光軸ズレに関しては、1つひとつの部品の累積誤差が原因で発生します。MKレンズでは、各レンズや移動群の誤差を修正するための調整機構を導入しています。これは従来のシネレンズや放送用TVレンズでも同様の機構を採用しており、その培ってきた製造技術をそのまま踏襲しています。
――FUJINONシネレンズの「HKシリーズ」、「ZKシリーズ」、「XKシリーズ」と色味を統一していますがどのように統一して、どのようなところに苦労しましたか?
田中氏(光学設計担当):レンズの色味はCCI(Colour Contribution Index)というもので数値化できるので、その数値を上位モデルと同じ範囲に合わせることで色味を合わせました。色味を合わせるためには、波長ごとの光の透過率をある値にしないといけません。それにはレンズの材質やコートの種類も関わってきますが、そういうところも考慮して上位モデルと同じ数値になるように工夫しました。
――MKレンズは操作感がスチルレンズと違うと感じますが、具体的にどのような点にこだわりましたか?
川村氏:トルクに関しては従来のFUJINONシネレンズに合わせています。フォーカスの回転角に関しては、回転角が小さいと少し回しただけで大きく移動してしまい、ピントが合わせにくかったりずれてしまいます。このような問題を回避するために、XKシリーズと同じ200°の回転角を実現しています。
野口氏:ちなみにHKシリーズのフォーカスの回転角は280°です。HKシリーズは基本的にツーマンオペレーションを前提としており、回転角の幅を広くしています。ZKシリーズやXKシリーズ、今回のMKレンズは、ワンマンオペレーションを前提としています。ワンマンオペレーションの場合は280°だと片手で回しきることができませんので、世界各国のカメラマンにヒアリングさせていただき、200°ぐらいが最適ということでこのようになりました。
川村氏:ギアリングに関しては、元々当社のシネレンズは上位機種も含めてすべて0.8Mで統一させていただいています。また、アイリスリングについてはシネ上位機種と同じ機構を採用することでシームレスな操作性を実現しております。
林氏(商品化担当):一番最後までもめたのはリングのトルクです。フォーカスリングのトルクは当初今よりも重かったですが、ワンマンオペレーションでカメラを持ってやるならばもう少し軽いほうがいいということになり、現在のトルクに変更しました。金属製外装の上位機種では従来実現していましたが、寸法バラつきが比較的大きい樹脂製外装では実現が困難で、追い込みに苦労しました。
リングの操作感に関しては、社内の3Dプリンタを活用しまして何パターンものリングを試作し、操作性の確認を行いました。実際にカメラマンに試用してもらい、「これはどうですか?」みたいな形で感想を聞いて、その答えを設計にフィードバックし、生産工程に落とす形で実現をしました。川村も工場に出張し最後までトルクの追い込みを行いました。
![]()
最終的に完成をしたフォーカス、ズーム、アイリスのリングの部品。リング部分は3Dプリンタで試作し、実際の使い勝手を検証しながら最終的な形状を詰めていった
武田氏(メカ設計担当):トルクで重要視したのはやはり作動感です。トルクは重さだけではなくて、ネットリ感みたいな感覚というのをシネレンズを使われてきたお客様は重視します。トルクの部分は特にスチルレンズと一番違うところで、単純な重さでありません。ネットリした作動感がポイントで、機構上の制約がある中でグリスの種類と塗布量、さらにはグリスを塗布する摺動部分の面積からも決まります。それが今まで我々がシネレンズや放送用のレンズで培ってきた技術のアドバンテージになると思います。そのへんのノウハウを活かしてMKレンズでもネットリ感のあるなめらかでざらつきのない操作感を実現できているかなと思います。
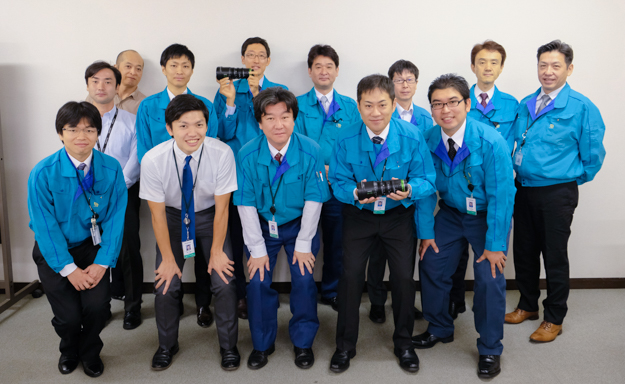
インタビューにご協力をいただきました商品企画、光学設計、メカ、光学技術、デザイン、営業担当の皆様
–ありがとうございました。

